Ultimate Guide To Spotting Faulty Welds
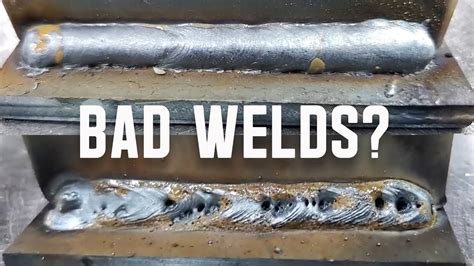
Introduction
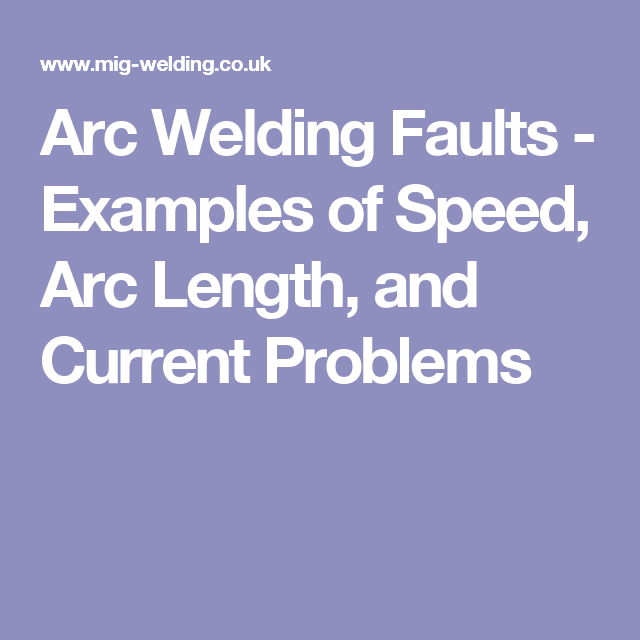
Identifying faulty welds is a crucial skill for anyone involved in the welding industry, whether you’re a welder, inspector, or quality control professional. Weld defects can compromise the integrity and strength of a structure, leading to potential failures and safety hazards. This comprehensive guide will equip you with the knowledge and techniques to recognize various types of welding faults and ensure the quality and reliability of your welds.
Understanding Weld Defects

Weld defects are imperfections or irregularities that occur during the welding process, resulting in a joint that fails to meet the required standards and specifications. These defects can arise from a variety of factors, including improper welding techniques, inadequate equipment, environmental conditions, or issues with the base material. It is essential to identify and address these defects to maintain the structural integrity and safety of welded components.
Common Types of Weld Defects
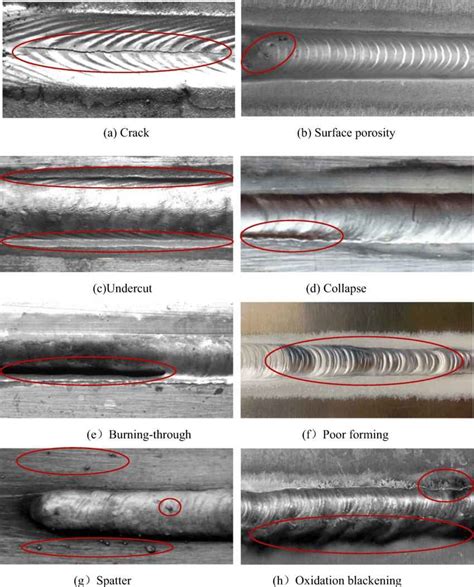
Incomplete Penetration
- Definition: Incomplete penetration occurs when the weld does not fully penetrate the joint, leaving a gap or lack of fusion between the base materials.
- Causes: This defect can be attributed to factors such as incorrect weld parameters, improper joint preparation, or an inadequate weld size.
- Visual Indicators: Look for a visible gap or lack of fusion in the weld, especially at the root or toe of the weld.
Porosity
- Definition: Porosity refers to the presence of gas pockets or voids within the weld metal.
- Causes: Porosity is often caused by trapped gases, improper shielding, or contaminants in the base material or welding environment.
- Visual Indicators: Porosity appears as small, round, or irregular holes on the surface or within the weld. It can also cause a rough or pitted appearance.
Cracks
- Definition: Cracks are linear defects that can occur in the weld metal or at the weld interface.
- Causes: Cracks may form due to high residual stresses, rapid cooling, or the presence of impurities in the base material.
- Visual Indicators: Look for visible cracks on the surface of the weld or within the weld bead. Cracks can be straight, branching, or have a random pattern.
Undercut
- Definition: Undercut is a groove or notch formed along the edge of the weld, reducing the cross-sectional area of the base material.
- Causes: Undercut can be caused by excessive heat input, improper welding speed, or incorrect electrode selection.
- Visual Indicators: Inspect for a visible groove or notch along the weld edge, typically appearing as a V-shaped indentation.
Inclusions
- Definition: Inclusions are foreign materials or particles trapped within the weld metal.
- Causes: Inclusions often result from contaminants in the base material, flux, or electrode.
- Visual Indicators: Inclusions appear as visible impurities or foreign substances within the weld, such as slag, flux, or metal particles.
Distortion
- Definition: Distortion refers to the deformation or warping of the welded structure.
- Causes: Distortion can be caused by factors like uneven heat distribution, excessive weld shrinkage, or improper clamping.
- Visual Indicators: Look for visible changes in the shape or alignment of the welded components, such as bending, twisting, or warping.
Burn-Through
- Definition: Burn-through occurs when the weld penetrates too deeply, resulting in a hole or excessive melt-through.
- Causes: This defect is often attributed to excessive heat input, thin base materials, or improper welding techniques.
- Visual Indicators: Inspect for a visible hole or excessive melt-through on the opposite side of the weld.
Lack of Fusion
- Definition: Lack of fusion is the absence of proper fusion between the weld metal and the base material.
- Causes: Lack of fusion can be caused by factors like inadequate heat input, improper welding speed, or dirty base material.
- Visual Indicators: Look for a visible gap or lack of bonding between the weld and the base material, often appearing as a thin layer of unmelted metal.
Slag Inclusions
- Definition: Slag inclusions are remnants of flux or slag trapped within the weld.
- Causes: Slag inclusions occur when flux or slag is not adequately removed from the weld during or after the welding process.
- Visual Indicators: Slag inclusions appear as visible particles or streaks within the weld, often having a different color or texture than the weld metal.
Cold Laps
- Definition: Cold laps are areas where the weld metal has not properly fused with the base material, resulting in a weak bond.
- Causes: Cold laps can be caused by factors like improper welding technique, inadequate heat input, or a lack of cleaning and preparation.
- Visual Indicators: Look for a visible layer of unmelted metal or a lack of penetration along the weld, often appearing as a flat or dull area.
Visual Inspection Techniques

Visual Examination
- Conduct a thorough visual examination of the weld, looking for any visible defects or irregularities.
- Use proper lighting and magnification tools to enhance your observation.
- Inspect the weld from various angles to identify defects that may not be apparent from a single viewpoint.
Surface Preparation
- Ensure the weld surface is clean and free from contaminants, such as oil, grease, or rust.
- Use appropriate cleaning methods, such as wire brushing, grinding, or chemical cleaning, to prepare the weld for inspection.
Magnification and Lighting
- Utilize magnification tools, such as magnifying glasses or microscopes, to examine the weld in greater detail.
- Provide adequate lighting to enhance visibility and identify subtle defects.
Documentation and Record-Keeping
- Document your inspection findings, including the location, type, and severity of defects.
- Maintain records of inspection results for quality control and future reference.
Non-Destructive Testing Methods

Ultrasonic Testing (UT)
- UT uses high-frequency sound waves to detect internal defects, such as cracks or porosity.
- It is a highly accurate method for identifying defects without damaging the weld.
- UT can provide detailed information about the size, shape, and depth of defects.
Radiographic Testing (RT)
- RT involves the use of X-rays or gamma rays to create an image of the internal structure of the weld.
- This method is effective in detecting a wide range of defects, including porosity, cracks, and inclusions.
- RT provides a visual representation of the weld’s internal structure, allowing for easy identification of defects.
Magnetic Particle Testing (MT)
- MT is used to detect surface and near-surface defects, such as cracks or lack of fusion.
- It works by magnetizing the weld and applying magnetic particles to the surface. Defects disrupt the magnetic field, causing the particles to gather and indicate the presence of a defect.
- MT is a sensitive method for detecting small cracks and surface irregularities.
Dye Penetrant Testing (PT)
- PT is a surface inspection technique used to detect surface-breaking defects.
- It involves applying a dye penetrant to the weld surface, which seeps into any surface openings. Excess penetrant is then removed, and a developer is applied to draw out the penetrant, revealing the defects.
- PT is effective in detecting cracks, porosity, and other surface irregularities.
Destructive Testing Methods

Macroetch Testing
- Macroetch testing involves etching a sample of the weld metal with an acid solution to reveal its microstructure.
- This method is used to identify defects, such as inclusions, porosity, or lack of fusion, within the weld metal.
- It provides a detailed visual representation of the weld’s microstructure, allowing for precise defect analysis.
Bend Testing
- Bend testing is a destructive method used to evaluate the strength and ductility of a welded joint.
- A sample of the weld is bent to a specific angle, and the resulting deformation or failure is assessed.
- Bend testing helps determine the weld’s ability to withstand bending stresses and identifies potential weaknesses.
Fracture Testing
- Fracture testing involves subjecting a sample of the weld to controlled loading until failure occurs.
- This method provides valuable information about the weld’s fracture toughness and the propagation of cracks.
- Fracture testing is particularly useful for evaluating the performance of welds under extreme conditions.
Welding Inspection and Quality Control

Welding Procedures and Specifications
- Establish and follow welding procedures and specifications that outline the required welding parameters, materials, and quality standards.
- Ensure that all welders are trained and qualified to perform the specified welding processes.
Welding Inspection Plans
- Develop comprehensive welding inspection plans that outline the inspection methods, frequencies, and acceptance criteria.
- Assign qualified welding inspectors to conduct inspections and ensure adherence to the inspection plan.
Documentation and Reporting
- Maintain accurate records of welding procedures, materials used, and inspection results.
- Generate inspection reports that document any identified defects, their locations, and the actions taken to rectify them.
Preventive Measures and Best Practices

Proper Joint Preparation
- Ensure proper joint preparation by removing contaminants, such as paint, grease, or rust, from the base materials.
- Use appropriate joint designs and fit-up techniques to facilitate proper weld penetration and fusion.
Welding Technique and Parameters
- Select the appropriate welding process and parameters, such as current, voltage, and travel speed, for the specific application.
- Ensure that welders are skilled and experienced in the chosen welding process.
Material Selection and Handling
- Choose high-quality base materials and welding consumables that meet the required specifications.
- Store and handle materials properly to prevent contamination or degradation.
Environmental Control
- Minimize the impact of environmental factors, such as wind, humidity, or temperature, on the welding process.
- Provide adequate ventilation and control the welding environment to prevent the accumulation of harmful gases or contaminants.
Post-Weld Cleaning and Inspection
- Thoroughly clean the weld surface after welding to remove any slag, spatter, or other contaminants.
- Conduct post-weld inspections to identify any defects that may have occurred during the welding process.
Conclusion
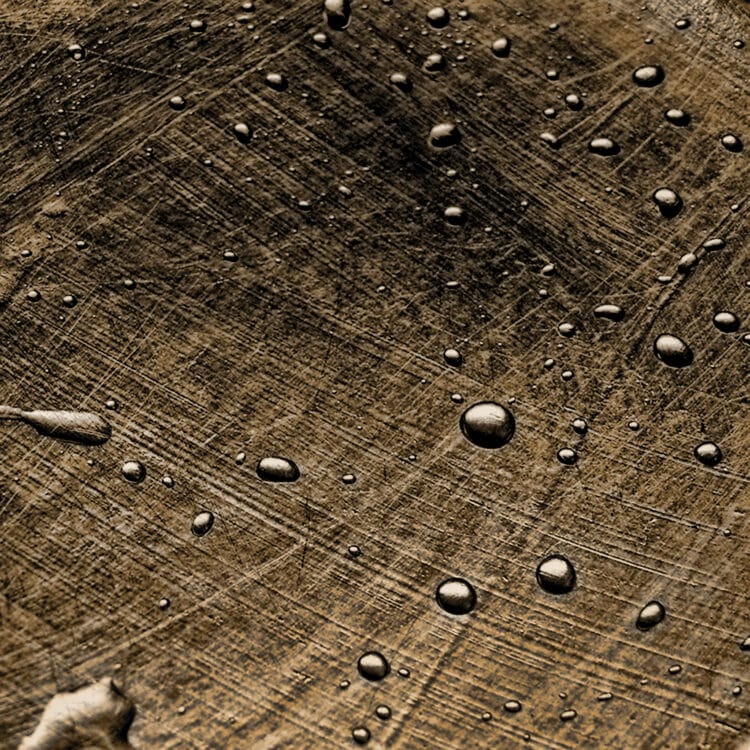
Spotting faulty welds is a critical skill for ensuring the integrity and safety of welded structures. By understanding the common types of weld defects and employing visual inspection techniques, non-destructive testing methods, and destructive testing methods, you can effectively identify and address welding faults. Implementing proper welding procedures, inspection plans, and preventive measures will contribute to the overall quality and reliability of your welds. Remember, regular inspection and attention to detail are essential in maintaining the highest standards of welding excellence.